Coal Slime Dryer
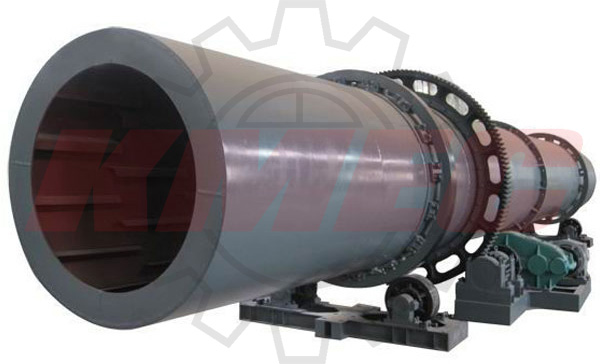
Featuring high moisture content and adhesive property, coal slime in the process of drying will be taken to the scattering system by the bond conveyer, and then the scattered material will be taken into the dryer full of negative pressure, after which the drying will be divided into several steps as follows:
Process Flow Diagram
- Guiding section. Upon entering into this section and blending with the high temp, negative pressure hot air, moist material will be promptly evaporated much and thanks to the shovelling plates, the material is tough to be bond together but led into next section.
- Cleaning section. Due to the work of shoveling plates, a vaporific curtain by the material will come into being and the drum internal walls will be bond with the material which will then be cleaned off swiftly by the cleaning device hereby, during which the coal slime lumps and agglomerates will also be crushed. Consequently, the heat exchange degree, ratio and the drying speed will all be increased.
- Shoveling section. Also called low temp drying zone. The coal slime hereinto remains slacked status with lower water content which means no possibility of bonding, however, after heat exchanging, the material will have met the requirement for water content and then go into next sections.
- Discharging section. Within the drying drum, there is no shoveling plate available. But the dried material will slide to the outlet.
- It consists mainly of such systems as heating, scattering, feeding, conveying, drying, dust collecting, electric controlling and crushing.
ⅡTechnical Parameters
Model/item | Drum inner dia. (M) | Drum length (M) | Motor power(kW) | Drum speed(r/min) | Overall size(L×W×H)(FOR REFERENCE) |
---|---|---|---|---|---|
GC-MNΦ1×8 | 1.0 | 8 | 5.5 | 3-6 | 8×1.9×2.1 |
GC-MNΦ1×10 | 10 | 10×1.9×2.1 | |||
GC-MNΦ1.2×10 | 1.2 | 10 | 10×1.9×2.1 | ||
7.5 | |||||
GC-MNΦ1.2×12 | 12 | 12×1.9×2.1 | |||
GC-MNΦ1.5×12 | 1.5 | 12 | 15 | 12×2.6×2.8 | |
GC-MNΦ1.5×14 | 14 | 14×2.6×2.8 | |||
GC-MNΦ1.8×14 | 1.8 | 14 | 14×3.0×3.0 | ||
18.5 | |||||
GC-MNΦ1.8×18 | 18 | 22 | 18×3.0×3.0 | ||
GC-MNΦ2×1.8 | 2.0 | 18 | 22 | 18×3.2×3.2 | |
GC-MNΦ2.2×18 | 2.2 | 18 | 30 | 18×4.0×3.8 | |
GC-MNΦ2.2×20 | 20 | 20×4.0×3.8 | |||
GC-MNΦ2.4×18 | 2.4 | 18 | 18×4.0×3.8 | ||
GC-MNΦ2.4×20 | 20 | 37 | 20×3.6×3.6 | ||
GC-MNΦ2.8×14 | 2.8 | 14 | 75 | 14×4.6×4.6 | |
GC-MNΦ2.8×18 | 18 | 18×4.6×4.6 | |||
GC-MNΦ3×20 | 3.0 | 20 | 110 | 20×5.0×5.0 | |
GC-MNΦ3.2×18 | 3.2 | 18 | 132 | 18×8.0×7.0 | |
GC-MNΦ3.2×20 | 20 | 20×8.0×7.0 |
Ⅲ Features
- The dryer possesses reliable overload capacity, also characteristic of larger throughput, lower fuel consumption and costs.
- It adopts concurrent drying method to flow hot air and moist material into the drum unanimously from the same side. During which the material will be evaporated so outstandingly that a higher thermal efficiency can be ensured, besides, the temp of the outlet stays relatively lower.
- In terms of distinct attributes of a variety of materials, the operation parameters shall be altered accordingly. Technically, the feedstock shall be dispersed thoroughly and stably in the drum cavity for a better heat exchange.
- The advanced feeding and discharging system remarkably shadows the conventional dryer resulting in material blockage, intermittent and uneven transmission or even back feed on one hand and effectively lowers the dust collecting load.
- The new inner structure strengthens cleanness and thermal conduct of the scattered material and also helpfully avoids material binding upon the drum walls. Apart from the above, the structure can adapt to harsher conditions as for water content and adhesive property.
- The newly developed dryer can realize almost zero horizontal drive so that the wheel wear will be reduced with the drum body working stable and reliable.
- Capitalizing on centre-adjusting jockey pulley, the dryer can align the rolling ring with the pulley in touching, therefore, wear and power consumption can both be decreased sharply.
- As required, granule size and the moisture content can be adjusted, that is, for the dryer coal slime, its moisture content remains below 8%, with the size also of 8mm.
- For coal mining industry, such material as coal slime, raw coal,clean coal after floatation, mixed clean coal.
- For architecture industry, such material as blast furnace slag, clay, limestone, stand, quartz stones.
- For ore selecting industry, such material as ore concentrate , slag and tailings.
- For chemical industry, such material as the non-thermal sensitive.